Let's figure it out together.
How to Produce Low-Density Physically Foamed Polyethylene (EPE): Myths, Limits, and Real Solutions
Reduce Raw Material Costs Without Compromising Foam Quality
In today’s highly competitive foam polymer market, manufacturers are constantly looking for ways to reduce production costs. One of the most common strategies is to reduce the density of expanded polyethylene (EPE) foam. Why? Because raw material costs can account for up to 55% of the total cost per square meter. Even a 10% reduction in weight can lead to significant savings.
But how far can we go without sacrificing product quality, mechanical strength, or dimensional stability?
But at the same time, how can we avoid ultimately getting an increase in technological defects associated with collapse, cell rupture, a decrease in the physical and mechanical properties of resistance to loads, etc. when reducing the density of physically polyethylene foam (EPE)? In addition, the question arises, what is the minimum density of the finished polyethylene foam product that we can obtain in the extrusion process so as not to have problems with quality later? Can we be sure that after a week of keeping the products in the warehouse we will not have to dispose of and granulate the entire batch or, even worse, pick up this defective batch of products from the customer's warehouse?
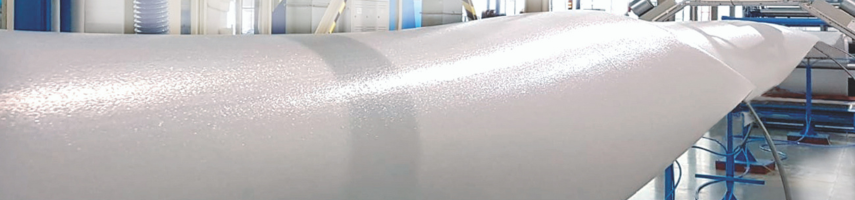
We often receive requests like:
"Can your extrusion line produce EPE foam with a density of 12 kg/m³ (0.75 lb/ft³) and still guarantee quality?"
"We bought a line recommended at a trade show, but we can’t achieve densities below 14 kg/m³ (0,87 lb/ft3). Can your engineers help us set it up properly?"
The purpose of this article is to clarify once and for all the TRUTH and the MYTH about the physical foaming of ultra-low-density polyethylene.
How to calculate the gas saturation coefficient of molten polymer and why it is impossible to cheat the laws of physics. Where is the limit of density reduction of physically foamed polyethylene and why most of the information on the market has nothing to do with REALITY.
Let’s be clear: producing physically foamed, closed-cell polyethylene with a density below 13–14 kg/m³ in a continuous extrusion process is a myth. Here’s why.
Let us remind you that we are talking exclusively about foaming polyethylene, polypropylene or polystyrene by extrusion and the solubility of liquefied hydrocarbon gases in them under pressure.
Yes, of course, various tests were carried out, such as obtaining physically foamed ultra-low density polypropylene in the range of 10 kg/m3 (0,62 lb/ft3) by one of the largest manufacturers of foamed polyethylene in the world, but these tests did not find industrial application, since the process is simply impossible to control on an industrial scale.
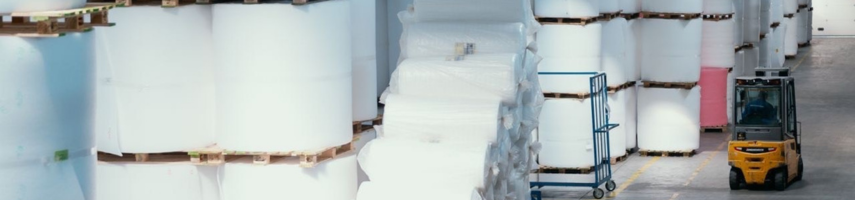
It is no secret that the low density of physically foamed polyethylene is achieved by solubility in the melt of the largest amount of foaming agent, in our case, a gas such as Butane. The higher the viscosity of the gas and the greater its volume retained in the liquid state inside the extruder, the better the gas is dispersed into the melt and a smaller volume of it evaporates when the polymer exits the foam extrusion head (foam extrusion die).
During the extrusion of low-density polyethylene, the melt temperature in the extruder reaches 160-180 °C (320-356 °F) degrees and at this temperature it is necessary to maintain a minimum melt pressure (> 50 bar) so that butane has sufficient viscosity in the "borderline" state in order to mix with the polymer melt.
The technology of twin-screw extrusion with counter-rotation from FAP is capable of maintaining such a high melt pressure regardless of the pressure in the foam extruder head (foam extrusion die) and that is why this technology, unlike the most common single-screw extrusion on the market, is capable of producing both very thin foams with a thickness of 0.3-0.5 mm (1/64-1/50'') and foams with a thickness of 25-30 (1-1,2'') mm on the single line.
But even the counter-rotating twin-screw extrusion technology from FAP, which is the best technology for physically foamed polymers today, has a limit in the volume of gas dissolved in the polymer and, accordingly, the weight and density of the finished foam product.
The Physical Limits: Why You Can’t Cheat the Laws of Physics
Let’s break it down with an example:
Producing physically foamed polyethylene (EPE foam) with:
- Thickness: 2 mm (1/12'')
- Width: 2 meters (6,6 ft)
- Density: 15 kg/m³ (0,94 lb/ft³)
Means dissolving about 4–4.5% gas into the melt. That’s already near the physical maximum for industrial processes. If you increase the gas content beyond this, you get: - Foam collapse
- Cell rupture
- Shrinkage during degassing
That is, if we take the volume of the polymer mass of 250 kg / hour in the extrusion process, we can dissolve in it only 10-11 kg of liquefied butane, taking into account the polymer processing temperature and the melt pressure both in the extruder and in the extrusion head. The rest of the introduced volume will evaporate during the foaming of the polymer with a sharp drop in pressure. Increasing the solubility of gas in the melt is complicated by the fact that it is necessary to both reduce the melt temperature to increase the viscosity of the gas and significantly increase the melt pressure.
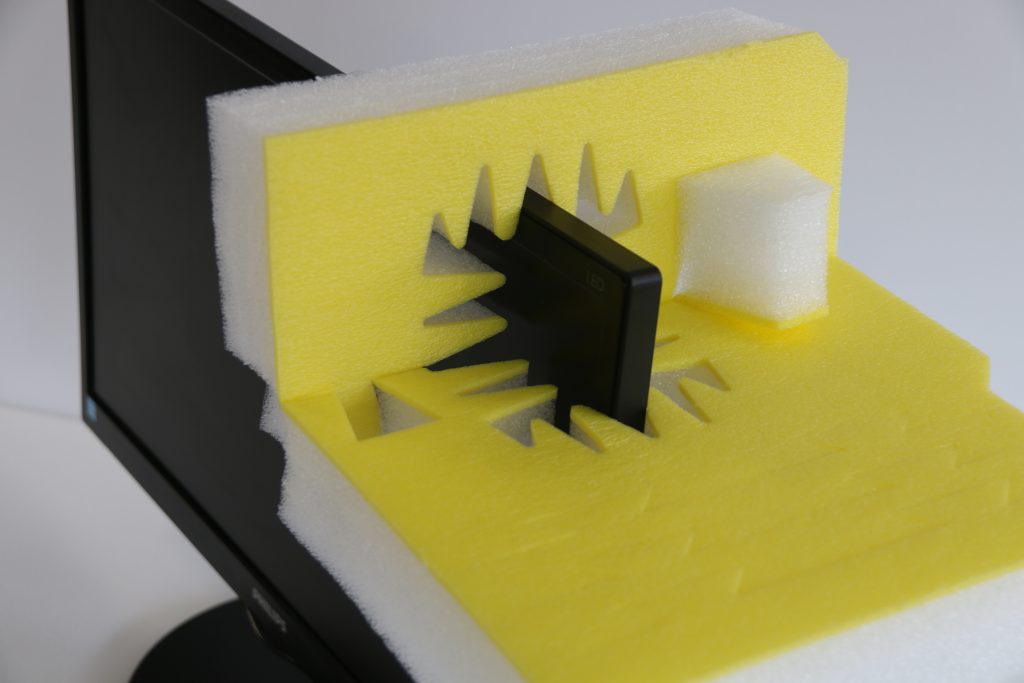
But when the melt temperature is reduced to increase the viscosity of the gas, the viscosity of the polymer also increases, making it difficult to disperse the gas, and in the case of increasing the temperature to reduce the viscosity of the polymer melt, even with an increase in the melt pressure, we increase the time for the crystallization of the polymer after foaming and thus the foam loses more gas during evaporation, which leads to partial collapse.
The second limitation is that with such a low density of foam plastic, the walls and edges of the cells are very thin and, accordingly, the risk of shrinkage, collapse of the foam plastic, or rupture of the cells during gas expansion is very high and is almost 100%. Such a low density is not a problem for open-cell foam plastics such as polyurethane, since there is not such a high pressure difference in the cells as in closed-cell foams. If we consider foamed polyethylene with a density of 12 kg/m3 (0,75 lb/ft3) during production, we will see that the foaming coefficient is 77.08, and the volume of the polymer itself per 1 m3 of foam (finished product) will be only 1.297%. As you understand, these figures are on the verge of fantasy.
To take wishful thinking as reality
Why Trade Show Samples Can Be Misleading
But how do we come across such light samples of physically closed-cell polyethylene foam at exhibitions? Today, more and more manufacturers declare such figures, misleading manufacturers. In fact, there is nothing unusual. As manufacturers, we measure the density during the production process, at the moment when the material is produced on the production extrusion line. But how does the density of foamed polyethylene change after the full degassing period, that is, when the butane inside each cell is replaced by air.
For visual calculations, let's take the same material of polyethylene foam with a thickness of 2 mm (1/12'') x a width of 2 m (6,6 ft) x a density of 15 kg / m3 (0,94 lb/ft3):
- The weight of one square meter of our material during the production process will be 31.8 grams,
- Based on the density of the dissolved gas and the warehouse temperature of + 15 °C degrees (59 °F), the weight of gas in 1 m2 (10,7 ft2) of material will be 4.05 grams,
- In the process of replacing gas with air for about 19-25 days, our 1 m2 (10,7 ft2) of foamed polyethylene will lose about 3.3 grams in weight, since the specific volume of air m3 / kg is 5.66 times higher than that of butane,
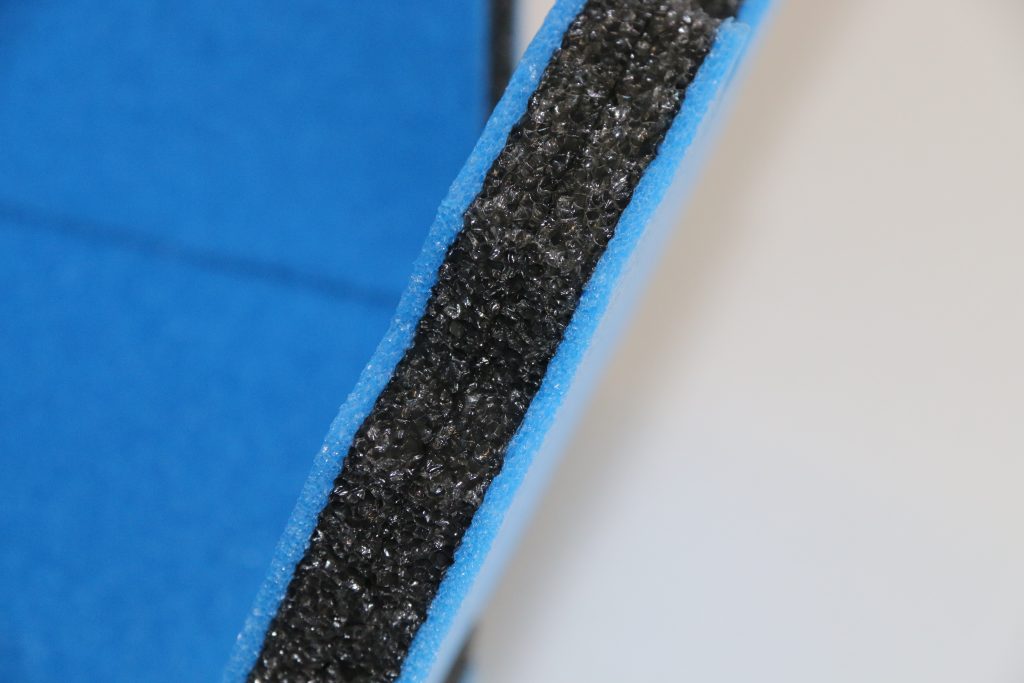
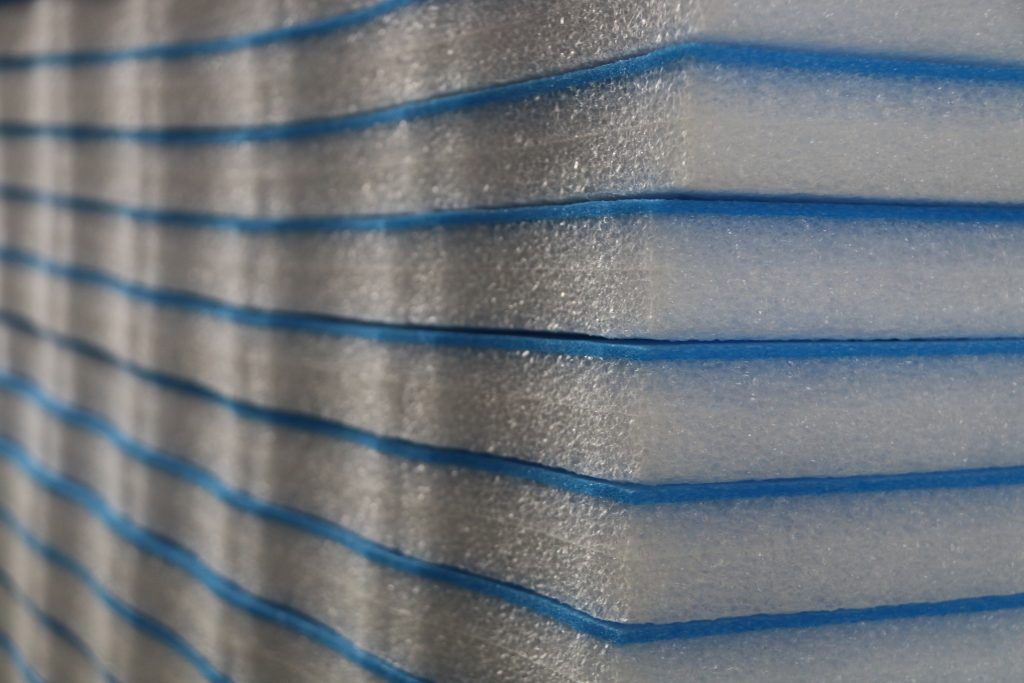
- As a result, after 19-25 days, 1 m2 (10,7 ft2) of our material will weigh approximately 28.5 grams, which is 10.4% lighter, and the density of this material will be 13.4 kg/m3 (0,8365 lb/ft3),
- And if we take the time for the gas to escape over 40-50 days, then the weight of our sample will change by as much as 14.5-16 % and, accordingly, the density will decrease and approach 12 kg/m3 (0,75 lb/ft3).
Thus, it is important to distinguish the time of measurements of the finished foam product and understand when these measurements were made.
At FAP, we believe in truth over marketing hype. Our goal is to help you find the most efficient and realistic production parameters for your application.
Why FAP Technology Makes the Difference
✔ Counter-rotating twin-screw extruders
✔ Higher melt pressure and gas solubility
✔ Reliable low-density production
✔ Technical support and process optimization
✔ Full control over foam thickness and quality
Need to reduce your EPE production costs safely?
Talk to our team. We’ll help you reach the lowest density possible — without sacrificing performance or quality.