Competitive advantages of FAP twin-screw extrusion technology
It is no secret that each technology has its own advantages and disadvantages. When deciding to invest in the production of polyethylene (EPE), polypropylene (EPP) foam and polystyrene (EPS) it is important to understand:
What materials do you want to produce on foam extrusion line?
- What physical and mechanical characteristics should materials foam have?
- How to achieve low production costs without reducing the quality characteristics of the foam material?
- In which markets are you planning to enter?
- Will you be competitive in these markets with your foam products?
The "predictability" and stability of the production process plays a very important role. It must be assured that the quality parameters of the product (geometric dimensions, product density, cell structure, maturation process of the product in the warehouse) will be unchanged in every production batch produced. The foam production line should be automated to reduce the influence of the so-called "human" factor on the technological process of foaming, and to make the production process itself safe and highly efficient.
In this article we will give some examples of the competitive advantage of FAP foam extrusion lines with counter-rotating technology for the purpose of comparison with single-screw extrusion technology. We focus exclusively on polyethylene and polypropylene foaming processes by direct injection of pressurized gas into the polymer melt (physical foaming).
Melting and mixing of process additives
In contrast to single-screw extruder technology, twin-screw FAP extrusion technology ensures uniform melt and mechanical mixing of the polymer by grinding of material at the screw contact point, rather than by creating melt back pressure as is the case with single-screw extruder. This positively affects technological factors such as:
- Reduces friction during the melting process and decreases the surface tension of the melt, which has a significantly better effect on the characteristics of the finished foam material, such as cell wall thickness and density, reduces % residual deformation in compression, and increases the dynamic modulus of elasticity of foams under load.
- Significantly improves the process of mixing in the melt of various components, such as dye concentrates, nucleators, sliding agents, flame retardants and others, which significantly reduces the time for changes in the recipe during foam production and reduces the amount of technological waste production. As example, the average time for complete mixing of colorant with the melt is no more than 7 minutes, respectively, and any technological adjustments made by the operator of the line in the production process, noticeable in no more than 5-7 minutes.
- There are no localized points of overheated polymer mixture because FAP's counter-rotating screw technology ensures that the melt is constantly turning, which contributes to more uniform cooling and stable behavior of the foamed polymer during degassing, minimizing the risks of overexpansion or cell collapse of the finished foam material.
Improved dispersion of gas in the melt
One of the main processes in the production of non-cross-linked physically foamed EPE, EPP, EPS is the mixing of the melt with gas. In the gas inlet area of the extruder, it is necessary to maintain the optimum pressure so that the gas is in the right state and has sufficient viscosity and density for dispersion and solubility in the molten polymer. But how does this affect the production process and the quality characteristics of the finished foam products?
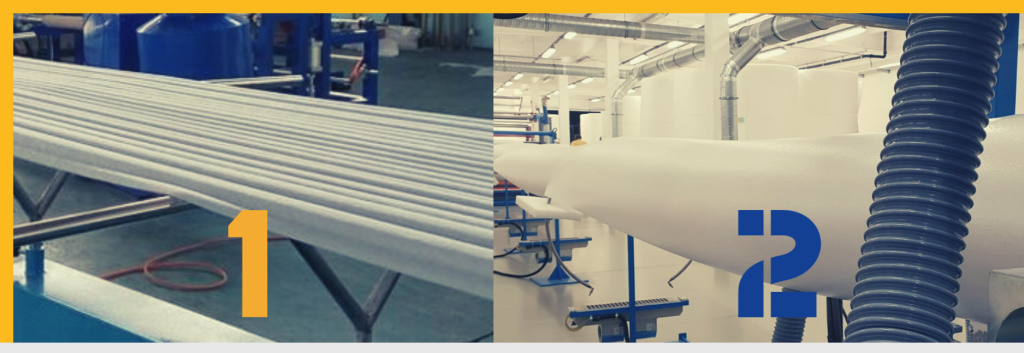
Photo 1. Production of 5 mm thick physically foamed polyethylene with high and frequent waves
Photo 2. Production of physically foamed polyethylene with thickness of 20 mm with flat smooth surface
Photo 1 shows a 5 mm thick polyethylene foam product produced on a single-screw extrusion line. The material has a fairly frequent and high wave. This is because, in order to pressurize and maintain the required pressure in the gas injection zone of the single-screw extruder, it is not possible to use a sufficiently low pressure at the die outlet of extrusion head and an extrusion head is designed in such a way as to create back pressure in the extruder barrel in addition to the filter screen. This severely limits the production process and makes it practically impossible to produce polyethylene foams with high thicknesses (e.g. more than 12 mm).
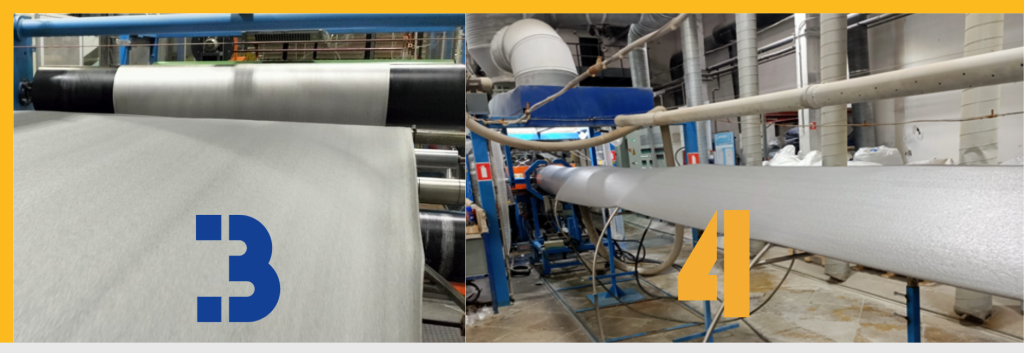
3/4. Production of 5 mm thickness low density polypropylene foam with flat smooth surface on extrusion line FAP.
FAP foam extrusion lines (photo 2,3,4) equipped with two screws with counter-rotating movement that allow to create sufficient pressure in the gas inlet zone of the extruder even at extremely low pressure at the die outlet of the extrusion head. In addition, the unique design of the screws of the gas inlet zone allows changing the flow of the melt direction and to create a stronger mixing effect, which in turn allows dispersing the gas in the melt much better and finally to obtain foam with a more homogeneous fine cellular structure (Microcell Technology). All this allows the production of foamed polyethylene and polypropylene both at critically high pressure and at sufficiently low pressure, with a finished product thickness from 0.5 mm to 25 mm, with smooth surface of low-density foamed polyethylene and polypropylene without waves on the same extrusion line. This creates significant advantages in the formation of production costs of finished foam materials for our customers and makes the technology of FAP extrusion lines universal from many sides.
The impact of FAP twin-screw extrusion technology on the cost of the end product
Due to the fact that FAP extrusion technology allows much better and faster cooling of the melt at start-up and adjustment of the extrusion line to the final product, faster and better mixing of colorants and additives due to mechanical contact and the unique screw design, it directly affects the cost of the finished product of polyethylene (EPE), polypropylene (EPP) foam and polystyrene (EPS). Stable production process, with controlled quality indicators, minimizes any risks of hidden defects of finished products, shrinkage of foam during degassing and violation of cell structure integrity, which generally affects production and cost of finished products.
Set-up time of FAP foam extrusion line from the moment of start-up to the first finished roll of EPE foam with thickness of 8-10 mm is on average not more than 65 minutes, which is about 15-20 minutes less than the time required for setting up EPE foam with the same thickness on a single-screw extruder with similar production capacity. This not only saves time and reduces the cost of power consumption, but also reduces the consumption of raw materials in the process of starting the line by 15-20%, affects the reduction of the minimum economically efficient production batch by 10-14%, as well as reducing the cost of placement and storage of products in the warehouse.
Advantages of FAP Twin Screw Counter-Rotating Foam Extruder
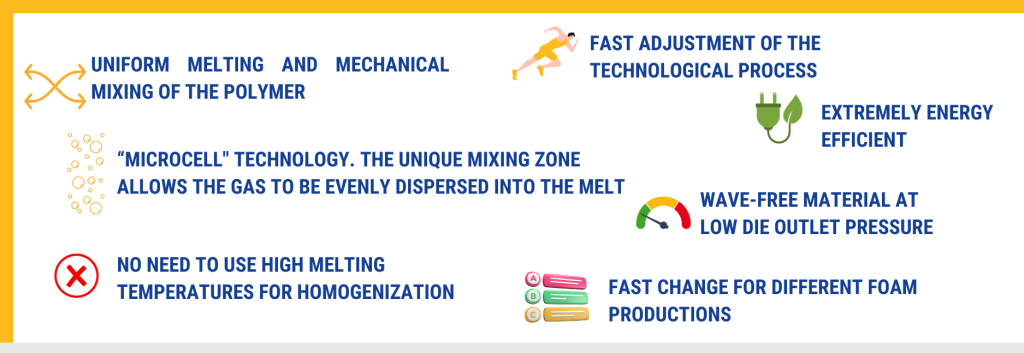