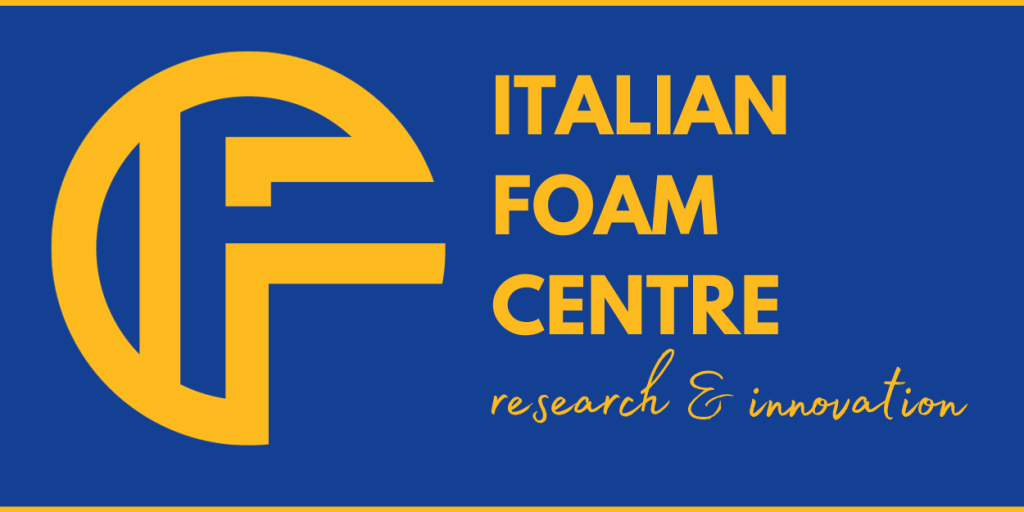
Analysis of the main problems in the production of foam materials around the World.
- Low automation of production processes.
- Bubbles, foam collapse, layer delamination during lamination, a lot of defects during production line setup.
- Degassing period, low warehouse turnover, the share of logistics in the cost price can be 18-23%.
- Lack of intellectual base and resources for developing new types of products.
- Big problems with qualified personnel.
- High costs of raw materials - the share of raw materials in the cost price is from 45 to 55%, therefore any price increase significantly increases the cost price of products.
Specific solutions from FAP division Italian Foam Centre
Challenge 1 - Technological Defects and Poor Quality of Foamed Polymers?
- Destruction of the structure and bubble formation on the foam surface during degassing?
- Low adhesion of foamed polymer and peeling of layers after lamination?
- High percentage of defects per batch during extrusion?
- Low compressive strength, poor thermal stability, insufficient tensile strength, or other unmet required parameters?
Solution 1 by Italian Foam Centre:
- Optimizing production process parameters through detailed analysis and specific recommendations for each type of processing additive.
- Developing and implementing copolymers in the production formula to enhance adhesion.
- Minimizing technological defects by improving technology and production processes.
- Enhancing the physical and mechanical properties of expanded polymers to meet customer requirements.
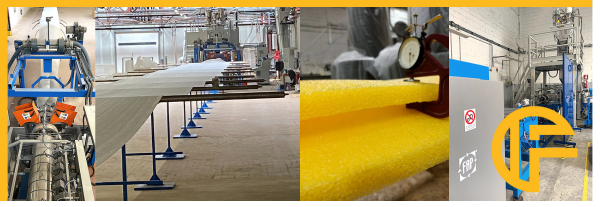
Challenge 2 - Struggling with High Raw Material Costs?
- Looking to reduce product density without compromising production stability?
- Unsure which raw materials to select for your specific product?
- Wondering if it’s possible to produce physically foamed ultra-low-density polyethylene?
Solution 2 by Italian Foam Centre:
- Conducting in-depth analysis of raw materials and equipment to optimize production costs.
- Developing tailored raw material specifications based on the type of product being manufactured.
- Proposing advanced technological solutions for producing physically foamed polyethylene with the lowest possible density while ensuring a stable production process.
Challenge 3 - Developing New Foamed Polyethylene and Polypropylene Products?
- Need to create a product that stands out against other polymers?
- Lacking knowledge of raw material compositions?
- No access to testing facilities?
- Ready to bring your product to market?
Solution 3 by Italian Foam Centre:
- Innovating new types of expanded polymers, including the blending of different polymers to introduce new properties.
- Developing the raw material base with detailed cost analysis tailored to your technical specifications.
- Testing production processes in FAP’s dedicated laboratory.
- Evaluating the product for compliance with the required physical and mechanical properties as per technical specifications.
- Providing comprehensive marketing support to promote your product within the packaging and insulation markets.
Challenge 4 - Advanced Training for Engineers and Operators in Polymer Foam Production
- Need to enhance the skills of your production team in polymer foam manufacturing?
- Looking to reduce human error rates in production?
Solution 4 by Italian Foam Centre:
- Developing comprehensive training materials for an in-depth understanding of physical foaming
- Organizing and conducting practical, hands-on technological training directly at your production site.
- Creating process documentation and operating procedures that align with the quality management system.
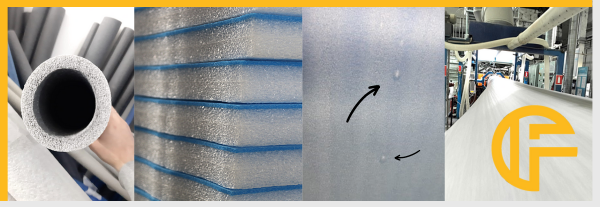