...and winding type plays an important role.
The process of gas substitution with air in closed cell foam with liquefied hydrocarbon gases (degassing process) is one of the most important processes, which is at the same time a "bottleneck" in the foam polymers productions. The degassing time of the foamed polymer directly affects both the final cost of the finished product and the manufacturer's responsiveness to customer orders, which is a very serious advantage in these highly competitive times.
But what dramatically affects the duration of the degassing process of physically foamed polyethylene (EPE) and polypropylene (EPP)?
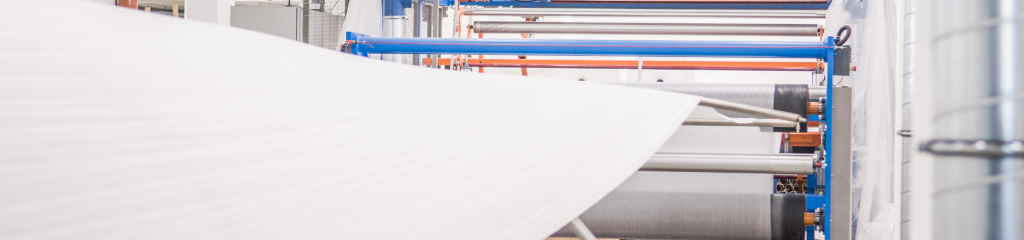
Glycerol monostearate or GMS
Glycerol monostearate GMS - belongs to esters, migrates to the foam surface, reducing friction and static charges on the foam surface. Like all migrating antistatic agents, GMS accumulates moisture on the foam surface and creates a very thin greasy layer. The quality and the amount of GMS required in the formulation can significantly affect the air permeability into the polymer and increase degassing time by 10 - 15% depending on the amount introduced.
Environment and air exchange in the warehouse
It's very important to maintain optimal temperature and humidity in the warehouse. For example, at a warehouse temperature of +25 °C the volume of air migration into physically foamed PE is on average 0,0030 grams/m2 per hour, while at a temperature of +5 °C this figure can be reduced to 0,0015 grams/m2 per hour. In southern countries with humid climates, the degassing process is usually faster, but it also often leads to rupture and collapse of the gas structural element.
The automatic winding machine
Unfortunately, there is no complete understanding of how important correct winding technology is in foam productions. In the process of winding roll, it is important to ensure that the foam tension does not depend on the diameter of the roll and that the core of the roll is not compressed. This is a very big problem for simple type winders. For this reason, each FAP winder is equipped with the so-called "Soft Winding System". This is a smart winding system that controls the equal tension of the winding rod for each running meter of material without creating a tightening effect on the core of the roll.
The creation of a small air gap between each wound meter of foam material allows to achieve a gas exchange air permeability of 0,0023 grams/m2 per hour even in the core of the roll, which is on average 0,0009 grams/m2 per hour more or 39% more than without "Soft Winding System" (calculations done at a temperature of +18 °C).
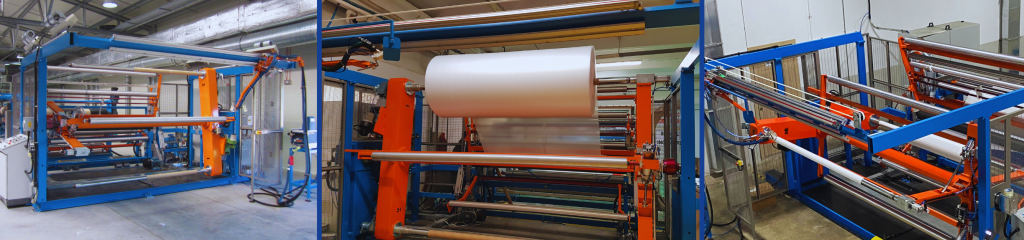