How much does it cost to produce an item?
To find it out, we have to consider: administrative costs; production costs; warehouse costs.
In this article, we will consider production costs, specifically those costs necessary to produce final products from expanded polyethylene (EPE) and polypropylene (EPP) foam.
The relevant factors to consider are:
1. Raw materials (usually represent 45-55% of the total cost of finished products)
2. Logistics (warehouse and storage)
3. Energy costs
4. Work productivity indicator
Market slowdown: cutting operating costs and reducing quality
The polyethylene (EPE) and polypropylene (EPP) foam processing sector is slowing down; some, even speak of oversaturation of the offer. To overcome this problem, manufacturers have often chosen to act on quality by: reducing product density, reducing nominal thickness, choosing low-cost raw materials. This strategy has enabled them to survive in the short run but cannot be considered a solution.
Solution: New processes to increase efficiency and reduce production costs
A key factor in the overall calculation of production costs for expanded materials such as polyethylene foam (EPE) and polypropylene foam (EPP) is the choice of equipment and process technology.
Reducing raw material costs with FAP’s twin-screw foam extrusion technology
Using low-cost technology may seem convenient, until we quantify how much it costs a company to produce 1 sqm of defective product.
An efficient production technology must guarantee:
- line start-up speed
- change of raw materials during the production process
- short time to change production parameters
- simplicity and precision of the line process control
Production advantages of FAP foam technology
In order to provide a technological advantage in production, FAP engineers design our lines with 4 fundamental characteristics:
- Dosing station
Equipped exclusively with independent gravimetric dosing units with a dosing accuracy of 0.3%, for the best control of the recipe (for checking the cost of raw materials per unit of product). The station is able to guarantee the change of any component during the production process in 7 minutes max. (for the minimization of production waste).
- Optimising warehouse stock management
Reducing production waste allows reducing inventories, increase stock turnover and obtain cost-effective batches, thus reducing product storage costs.
- Reducing the risk of overproduction
The twin-screw counter-rotating FAP foam technology significantly reduces:
- the risks of foam shrinkage due to the disruption of its cellular structure;
- bubbles on the foam material due to thinning of the cell walls;
- excessive gas expansion.
This eliminates the risk of products "overproduction", which would also affect their storage costs.
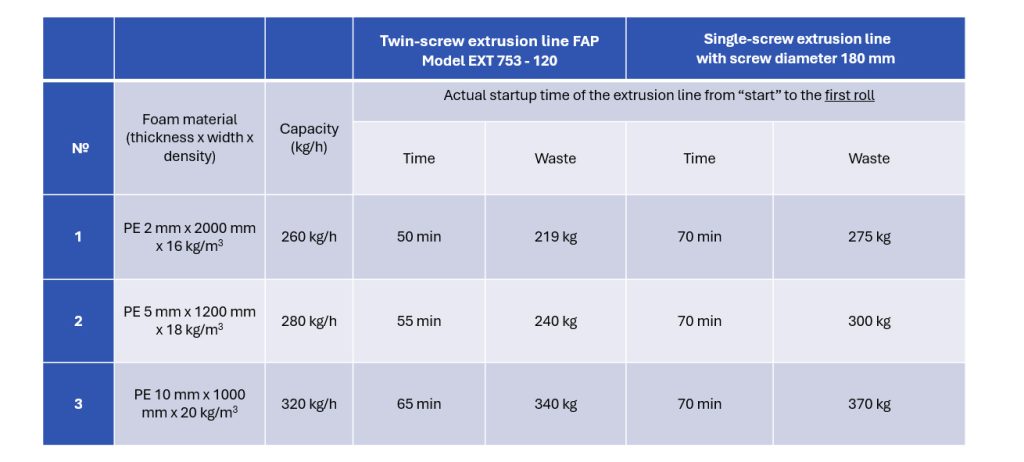
FAP extrusion lines: increasing energy efficiency
The cost of energy is rising: in many countries, in recent years, it has doubled. It is evident that this item has a great influence on production costs. This is why FAP complies with the highest and strictest energy efficiency standards by designing with specific attention:
- the heating elements: FAP extruders are shorter and more compact than single-screw extruders and consume 25-30% less electricity to heat the cylinder;
- the main motor: ABB's unique SynRM jet-rotor motors with energy class IE5 provide high specific power and torque and low winding and bearing temperatures, thus reducing energy consumption by 25-30% compared to standard induction motors;
- the gearbox: the modern Zambello ZT3 gearbox guarantees a high transmitted torque density (up to 17 Nm/cm3 per shaft).
FAP foam extrusion lines are some of the most efficient in terms of energy consumption per unit of production and provide huge cost savings.
Automation of FAP extrusion lines increases productivity and efficiency
Industrial automation processes are more important today than ever before: production lines must be intuitive in order to simplify the training of operators and quickly train new ones, but they must also be able to independently (automatically) perform numerous technological tasks.
The automation of FAP foam extrusion lines can be implemented in modular way and allows you to:
- visualize the progress of the production process in real time;
- receive control alerts;
- operate with automatic winding systems with soft winding technology;
- take advantage of systems for the automatic removal of the roll from the rod and for the automatic application of glue to the core.
By minimizing the number of operations on the line performed directly by operators, it is possible to significantly increase labor productivity in production, thus positively influencing the cost of finished products.