At FAP, we understand that the extrusion of gas-filled polymers is a critical process requiring precision and the right equipment. However, the lamination of physically foamed materials is equally important. This process involves bonding foamed polymers either to themselves (to increase thickness) or to other materials like reflective foil, PET, and HDPE, enhancing the final product's physical and mechanical properties. Our Laminator models has been specifically developed to ensure optimal lamination results, guaranteeing both flexibility and high performance in this delicate phase.
Though lamination might seem simple, it has many nuances that can affect the final product's quality, productivity, workplace safety, and production costs. What technical features of the equipment can be both an advantage and a significant drawback? Here’s what manufacturers and / or "converters" should consider when selecting equipment for laminating physically foamed polymers and bubble wrap:
- Hot Roll Heating System: How was the Teflon applied? How is the "hot" Teflon roll heated? What is the longevity of the Teflon coating?
- Air Blade Design: Is the airflow evenly distributed? What is the risk of material delamination?
- Safety and Automation: What safety and automation systems are in place? How efficient is the operator’s time and energy in producing one unit of quality product?
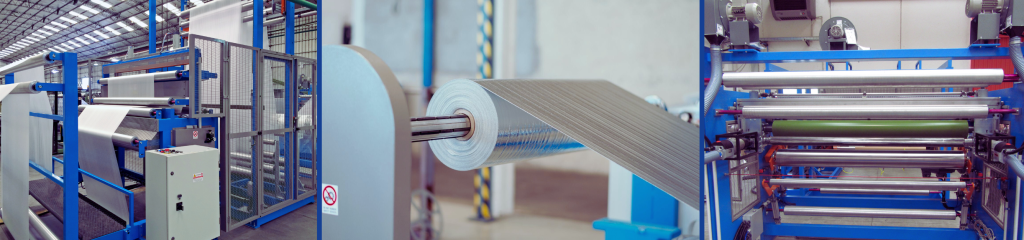
Why Do Most Foamed Polymer Manufacturers in Europe and Beyond Choose FAP Hot Laminators?
For nearly four decades, FAP’s closed-cell foam polymer lamination technology has been trusted in Europe, North, and South America. Continuous improvement by our team of engineers and technologists, combined with a deep understanding of critical processes like "degassing" of physically foamed polymers and adhesion changes under complex esters and antistatic agents, allows us to create unique and high-quality lamination lines.
What sets FAP hot laminators apart to drive manufacturers to choose them?
- Advanced Heating System: FAP’s lamination lines feature a hot oil temperature regulation system for the Teflon roll, maintaining temperature within +/- 1 degree Celsius. This eliminates risks of deposits, heat loss, and uneven surface temperatures.
- Special design of Air Blade: Our unique air blade design evenly distributes hot air, ensuring consistent adhesion during lamination. Adjustable air blade positions further enhance the production process.
- Reliable Components: We use only the most reliable components from international brands like Siemens, ABB, and Leister.
- Efficient Winding Systems: Our lamination lines include winding devices with automatic rod rotation and a unique "soft winding" system.
- Non-Stop Production due to High Automation Levels: Accumulators allow for changing the foamed semi-finished product without stopping the line.
- Safety Systems: Our unwinding, cutting, and heating elements meet all certification requirements, ensuring a safe production process.
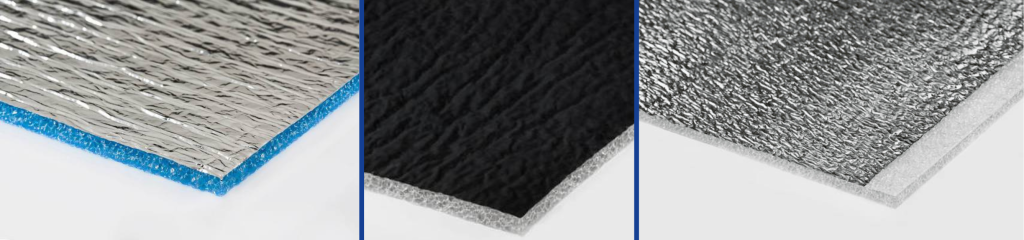