In today's rapidly evolving industrial landscape, businesses are under increasing pressure to invest in innovative technologies to meet market demands. At the recent SABIC Conference, we had the honor to present insights on how machine design is transforming the foam industry to meet pressing market demands like sustainability, cost efficiency, and product innovation.
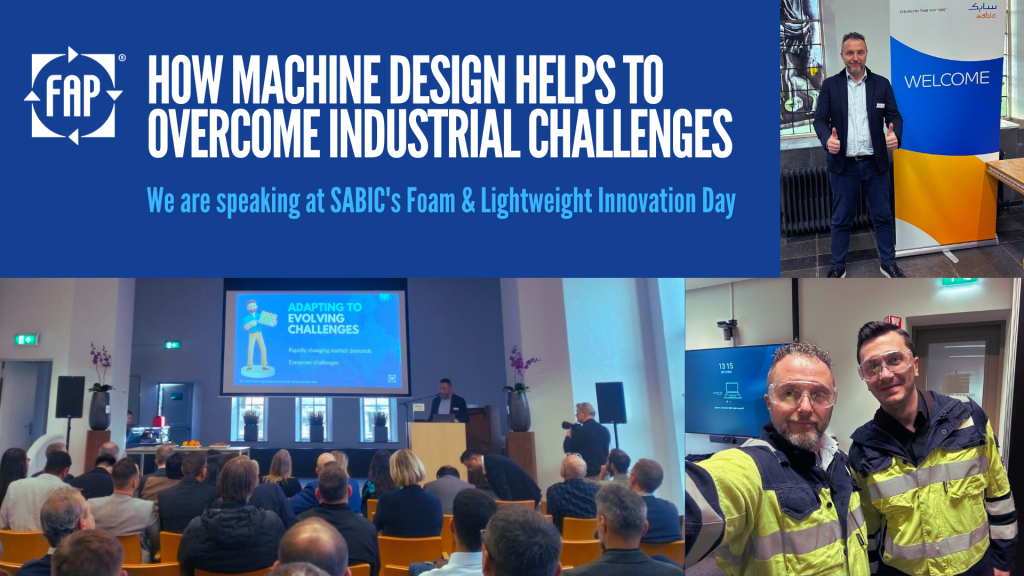
The European market, in particular, is shaped by clear trends: prioritizing sustainability, offering recycled and recyclable products, and enhancing competitiveness.
However, companies face significant hurdles, including higher labor costs, volatile raw material prices, and fluctuating energy costs, all of which squeeze profit margins. At FAP, we embrace these challenges head-on, focusing on how extrusion machinery is evolving to meet the demands of today and tomorrow. Let’s dive into the world of polymer foams, the challenges they present, and the cutting-edge solutions we’ve developed.
The Role of Polymer Foams in Everyday Life
Polymer foams have been indispensable in various applications for years, from acoustic and thermal insulation to food packaging. Imagine enjoying authentic Italian gelato stored in an XPS foamed container - an everyday example of how foams enhance quality of life. These versatile materials are made primarily from polymers like PP, PE, and PS, using physical expansion (with CO2) or chemical expansion methods to achieve their unique properties.
Addressing Key Challenges in Foam Production
Sustainability and Recyclability
The global push toward sustainability demands recyclable products. While physical foaming offers this advantage, chemical foaming renders products non-recyclable. The market already favors recyclable solutions, and soon, clear labeling will classify products as "green" (recyclable) or "red" (non-recyclable).
But the journey to sustainability isn't without challenges. Incorporating recycled materials into production introduces variability in material properties, leading to uneven density, foam collapse, and increased waste. Dispersion of recycled granules and gases within the melt remains a critical hurdle.
Competitiveness and Cost Efficiency
Market pressures often lead clients to ask: “Can you lower your price per square meter?” With labor costs fixed, the focus shifts to reducing material and operating costs. Traditional extrusion processes lack precise energy monitoring, and inefficiencies during startup or material change increase expenses.
Turning Challenges into Opportunities
At FAP, we are dreamers - and our mission is to turn dreams into reality. Our innovative extrusion technologies empower companies to achieve their goals by addressing these challenges with tailored solutions.
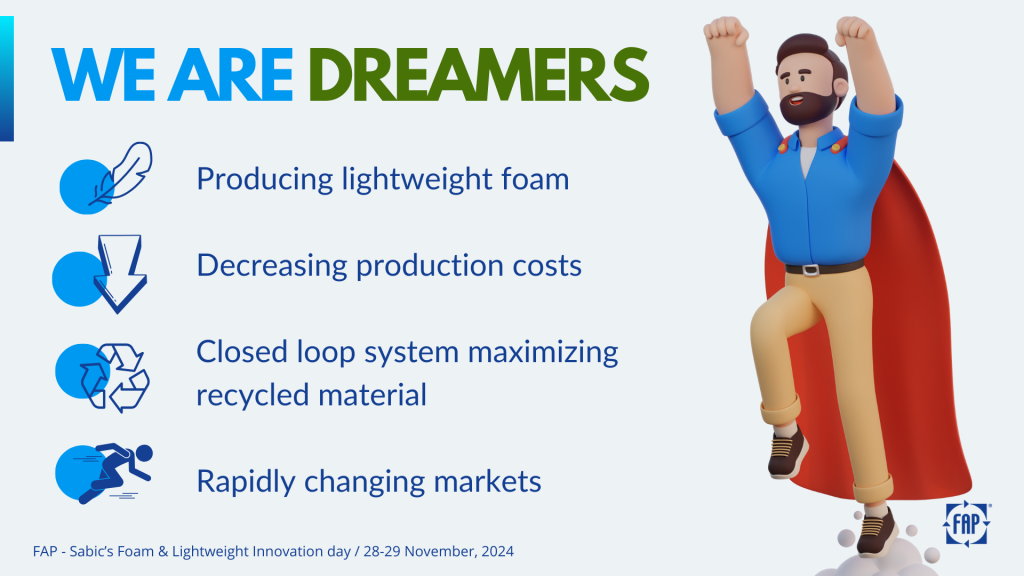
Key Innovations in Foam Extrusion Technology
- Lightweight Foam Production: Reducing raw material usage while maintaining quality significantly cuts costs.
- Maximizing Recycled Material: Our extrusion technology enables the use of recyclable and recycled materials, meeting both legislative requirements and sustainability goals.
- Adaptability for Fast-Changing Markets: With a single machine, clients can produce a wide range of densities and foam thicknesses, reducing the need for multiple investments.
Our Certain Vision for the Future: Two Scenarios
Scenario 1: Limited Progress
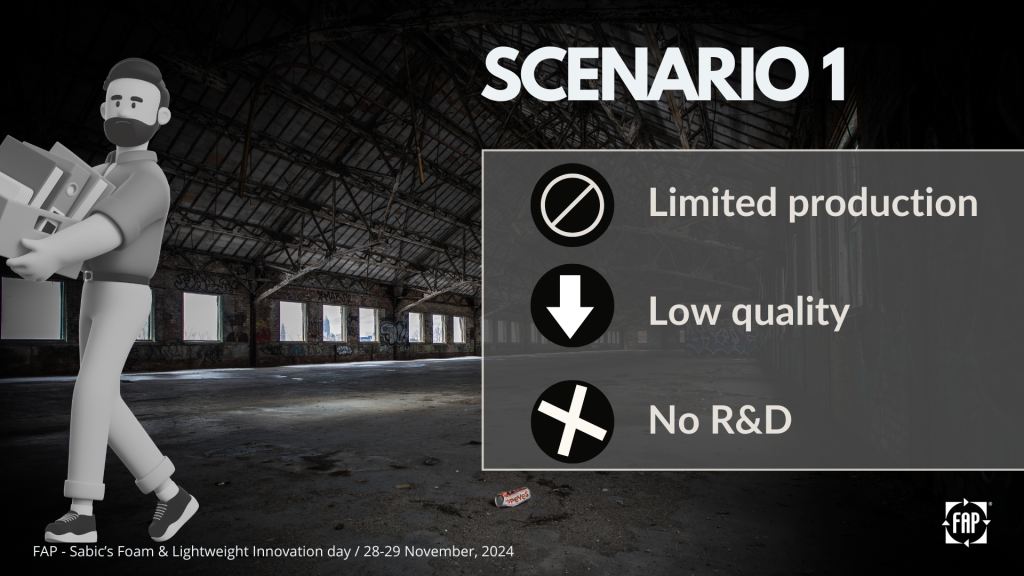
- Restrict physically foamed polymers to basic applications like packaging and insulation.
- Compete solely on price, risking poor-quality products that fail to meet consumer expectations.
- Deprioritize R&D, potentially losing valuable team members and innovation opportunities.
Scenario 2: A Path to Excellence
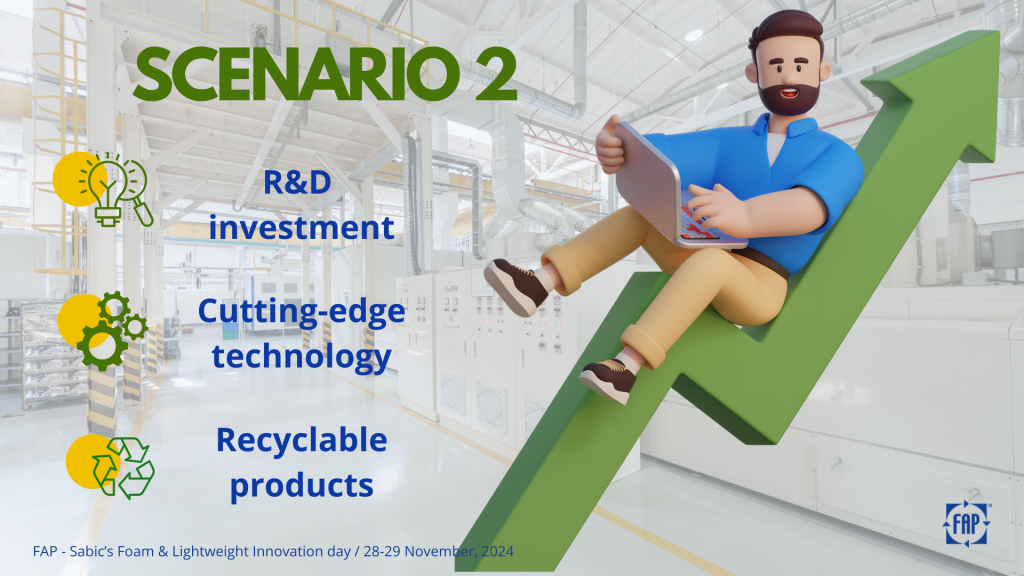
- Develop advanced extrusion technologies for 100% recyclable polymers with enhanced properties.
- Leverage state-of-the-art machinery to minimize waste, reduce production costs, and boost productivity.
- Collaborate with dedicated R&D teams to stay ahead of market demands.
For those who choose the second path, FAP offers groundbreaking solutions.
The Power of FAP’s Twin-Screw Counter-Rotating Extruders
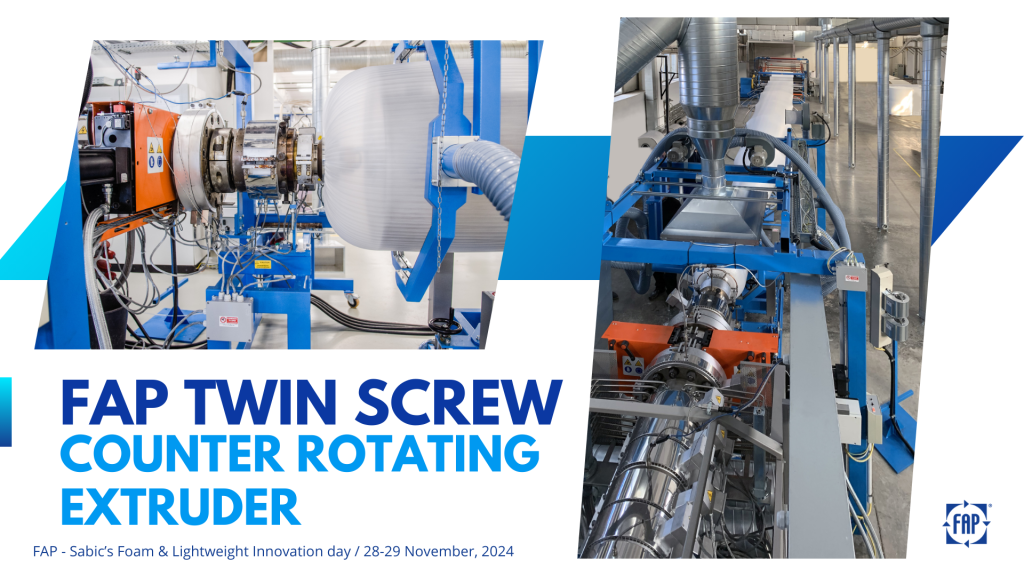
Our twin-screw counter-rotating extruders redefine material homogenization. The counterrotation creates dual mechanical shear stresses, ensuring uniform dispersion of additives and gas. This process enhances foam cell formation, delivering products with superior physical properties.
By applying high pressure to molten polymers, we increase gas solubility, achieving recyclable foams with exceptional thermal stability, compressive strength, and low density. These properties rival those of traditionally non-recyclable, chemically foamed products.
Incredibly Flexible Production with One Single Machine
Flexibility is key in today’s market. FAP technology enables clients to produce foam thicknesses ranging from 0.3 mm to 25 mm using the same machine. Additionally, our extruders support diverse polymer compositions (e.g., PP+EVA, LDPE+MLLDPE), offering unparalleled adaptability to market demands.
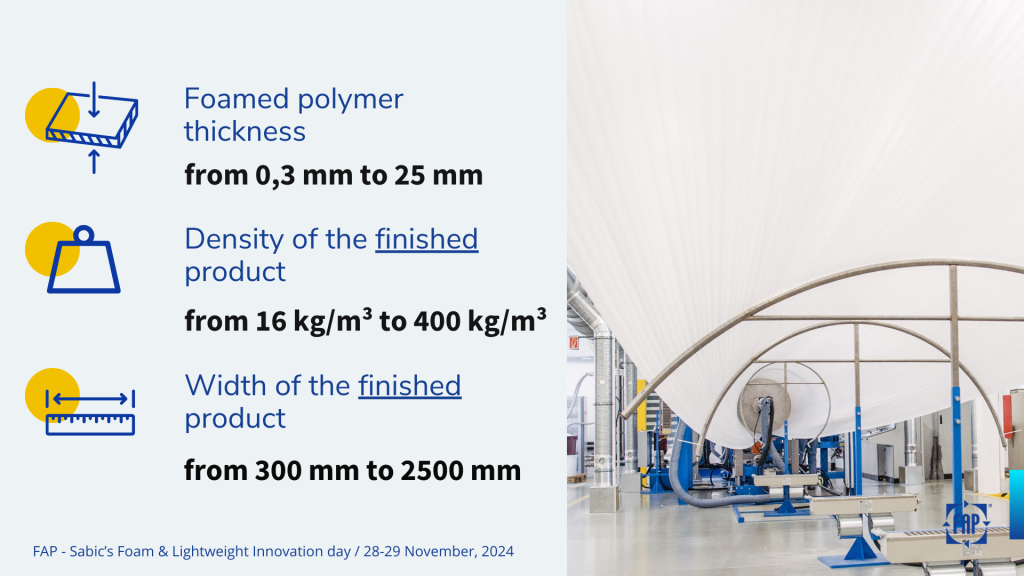
Our commitment to innovation is embodied in the Italian Foam Centre for Research & Innovation, where we explore new materials and optimize processes to push the boundaries of foam technology.
Game-Changing Packaging Solutions: The "Soft Winder"
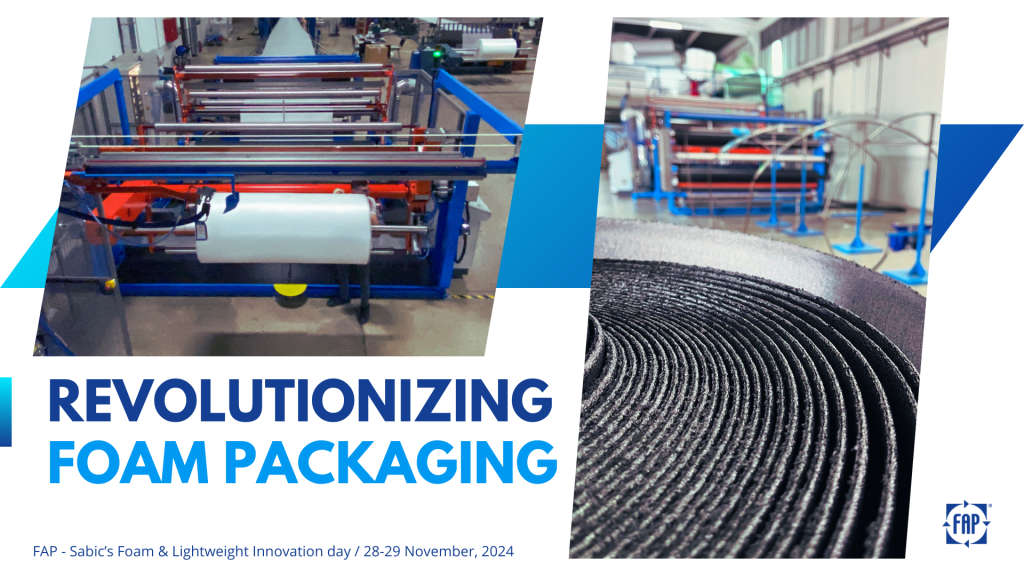
Packaging is critical in foam production, ensuring product quality during transport. In the 1990s, we revolutionized the process with our Soft Winder system, which:
- Reduces material degassing time by 40%.
- Minimizes production cycles and warehousing costs.
- Ensures uniform roll thickness for consistent expansion rates.
This innovation has cut raw material costs by 6% per square meter, delivering both quality and cost-efficiency.
Embracing Recycled Content
For foam thicknesses above 8 mm, we have achieved the use of 100% recycled PIR material without any virgin resin. Our clients integrate up to 30% PCR content using highly selected and filtered scraps, further advancing sustainability.
Economic Efficiency: The Final Frontier
Our "smart" cooling systems and advanced thermoregulation reduce startup times by up to 60 minutes and process waste by 30%, saving up to € 400 per startup. Pressure control across screw sections enhances energy efficiency, lowering energy consumption by 44% compared to traditional systems.
Building the Future, Today
At FAP, we don’t see problems - only challenges waiting for solutions. Our commitment to innovation ensures that what once seemed like a dream becomes reality. From 100% recyclable foams to cost-effective, high-performance machinery, we are transforming the foam industry.
If you share our vision for a sustainable, productive future, let’s start a partnership. Together, we can turn dreams into reality.
Contact us or visit our R&D center to discover how FAP can empower your business.