A WIDE-RANGING INTERVIEW WITH FABRIZIO POLI, CEO of FAP, WHO RUNS THIS FAMILY FIRM TOGETHER WITH HIS BROTHER FRANCESCO, THE SALES DIRECTOR.
The best advertisement for FAP has always been innovative, high-quality machines, on which clients can build the success of their enterprises.
These are words of Luigi Poli, who in 1987 founded FAP, a company based in Besana in Brianza (Monza Brianza) that builds extrusion plants and specializes, in particular, in systems for producing foam film. His words perfectly encapsulate the philosophy that, stemming from the typical Brianza mindset (a trait recognized both in Italy and internationally), has always guided this company. Indeed, Brianza people are committed to their work, even when the going gets tough, and they regard their products as the best possible testimony both to themselves and to their businesses.
In 2020, the reins of the company passed to Fabrizio and Francesco Poli. The two brothers both joined the family firm when they were very young. Accordingly, after lengthy “apprenticeships” in the various departments and in various roles, they are now entrepreneurs with considerable experience to bring to bear, despite their still relatively young age. Today, they are engaged not only in the day-to-day running of the company, but also in a drive to raise the level of every aspect of its operations through major investments of the kind that, especially right now, demand a good deal of courage and expertise. Clearly, two brothers have both these qualities in spades. To get all this straight from the horse’s mouth, we interviewed Fabrizio Poli. Our thanks go to him for giving us his time. This is what he had to say.
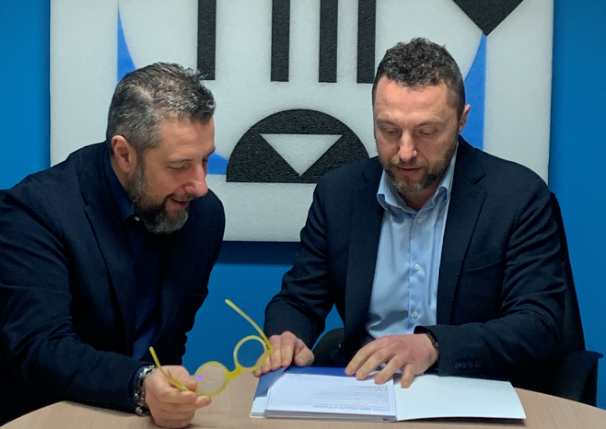
Let us start by talking about your specialisation, namely the construction of lines for the extrusion of foam materials. Could you outline the state-of-the-art in this field and your own most recent technological developments?
“FAP has over thirty years’ experience in the foam film sector. Through our research and development laboratory in France, we study new applications made possible by materials that have yet to reach the market, so that our technology can be made suitable for processing them. In other words, we always try to anticipate the needs of processors and the market, to be sure we are ready”.
Has Industry 4.0 changed the plants you build and your company’s internal processes? If so, how?
“For years now, the manufacturing sector has been going through an unprecedented process of transformation thanks to technologies such as robotics, artificial intelligence and augmented reality. At FAP, we have invested heavily in Industry 4.0, improving both access to data and the management of the extrusion process, so as to allow our customers to become more competitive, especially in terms of efficiency, precision and reduction of production costs”.
How is your reference market faring in these difficult times?
“We experienced a slowdown in March 2020 but bounced back almost immediately. Even though all sectors have been impacted by the Covid-19 crisis, fortunately our customer base is made up of companies that operate across a range of different ones, and have therefore felt the effects of this difficult situation less than they might otherwise have done. Thanks to their very high technical performance levels, foam films are used widely in numerous industrial fields, such as packaging, construction and the automotive industry. What is more, as an effect of imminent restrictions on the marketing and use of food containers made of polystyrene foam, we are seeing an increase in the demand for 100% recyclable solutions from food companies that are going to have to replace their products in polystyrene foam. We are therefore carrying out numerous tests in our laboratory in order to be able to offer our customers the best solutions to do just this. Our estimates suggest that 2021 will see our turnover further increasing on previous years”.
Speaking of Covid-19, what repercussions has the pandemic had on you, and how did you organise your work in the face of the emergency? Did you have to close or reorganise your production in any way?
“We closed the company in April 2020. At that time, of course, there was widespread fear, a lack of PPE, and no clear indications on the issue of workplace organisation. For us, like all companies, prioritising the health of our employees and collaborators has meant reorganising things, in other words, redistributing work spaces, sanitising common areas, making sure everyone has access to PPE and sanitising gels, and setting up training courses on safety protocols to follow within the company”.
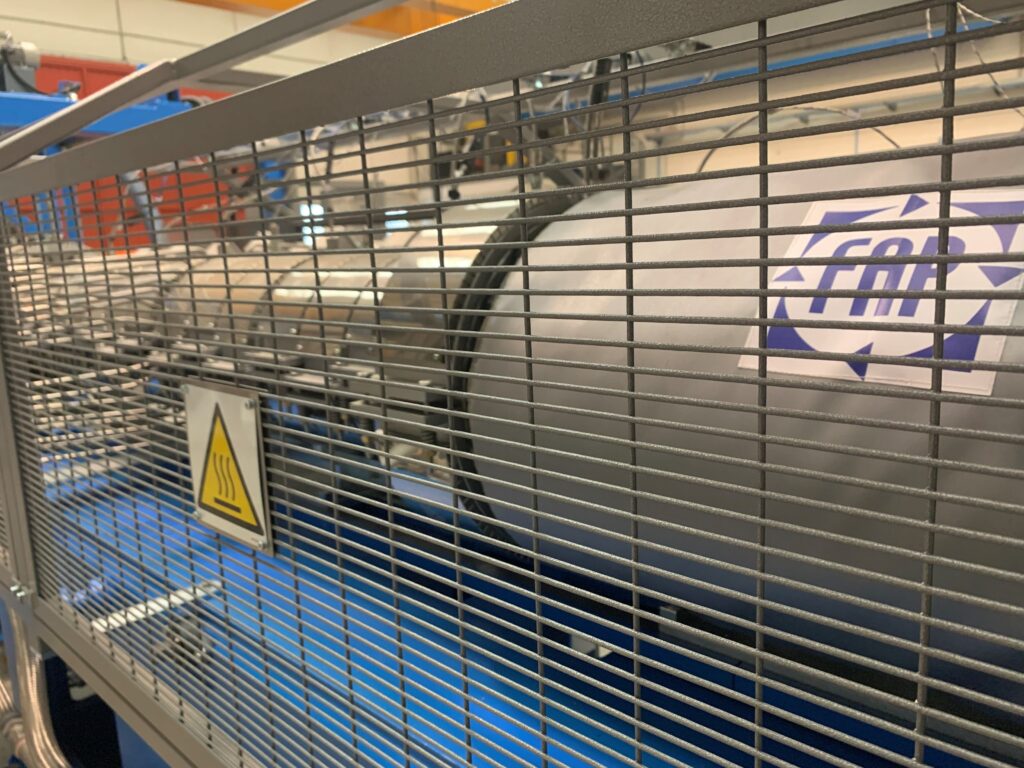
Could you tell us about your investments in the renovation and expansion of your factory? What stage are you at, and what interventions are planned?
“Work on our new production site, which will also be in Besana in Brianza (Monza Brianza), is scheduled to begin in July. The project involves expanding the production area, which is now insufficient to manage our ever-increasing number of orders. Furthermore, we will be moving our research and development laboratory to Italy, thereby expanding our international research centre here”.
You have recently undergone an image and communications makeover. Could you tell us more?
“We are a serious company, committed to our customers, and this, together with our achievements, says a lot about us. However, we wanted to make sure our story also reaches those who still don’t know us. It has always been widely accepted that a company’s logo is an essential element in defining its image. We have therefore had ours restyled and also given our website a makeover, to make it simpler and more modern. We are very pleased with the result and feel that our new logo really reflects what we are today: a dynamic family business with a long history of success, as well as solid and constantly growing international experience”.
These new investments suggest that you are really striving to forge ahead with your business. Will this drive include the recruitment of new technical and sales staff?
“We have already embarked on a quest to find new people to add to our R&D and technical teams. We have started this process early because we attach great importance to the recruitment side of things. After all, the daily efforts of our staff are the foundation of the company’s success”.