Why is it so important to choose the correct GMS dosing during the foaming/expansion process to produce high quality PE (polyethylene) or PP (polypropylene) foam material?
Simply because GMS, being an emulsifier and one of the most significant components, has a huge influence on many factors.
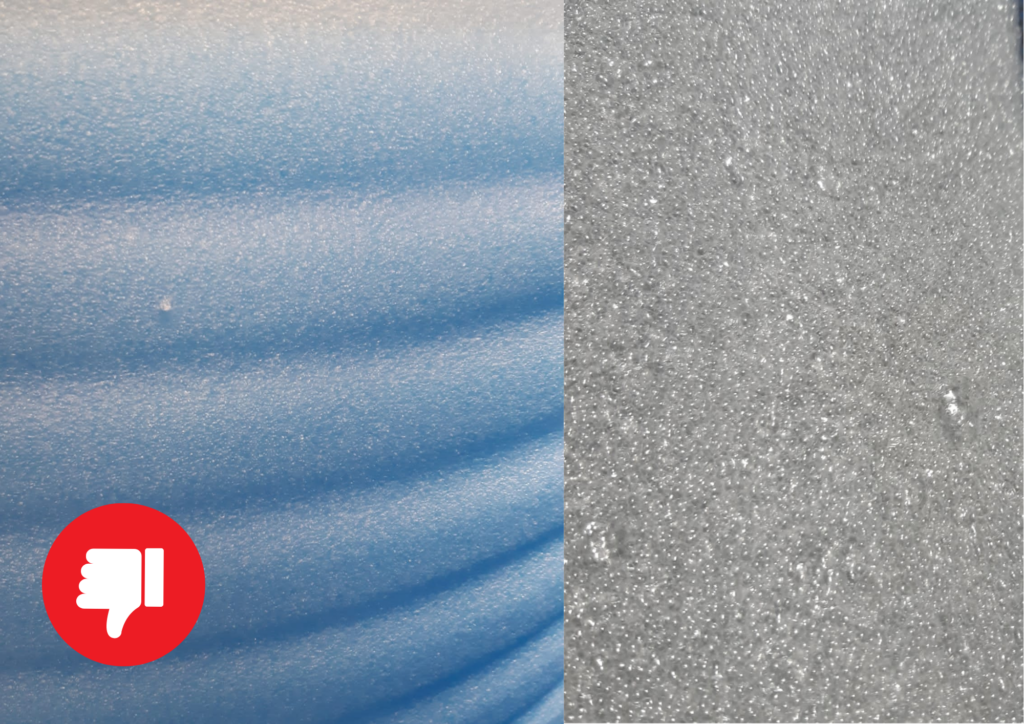
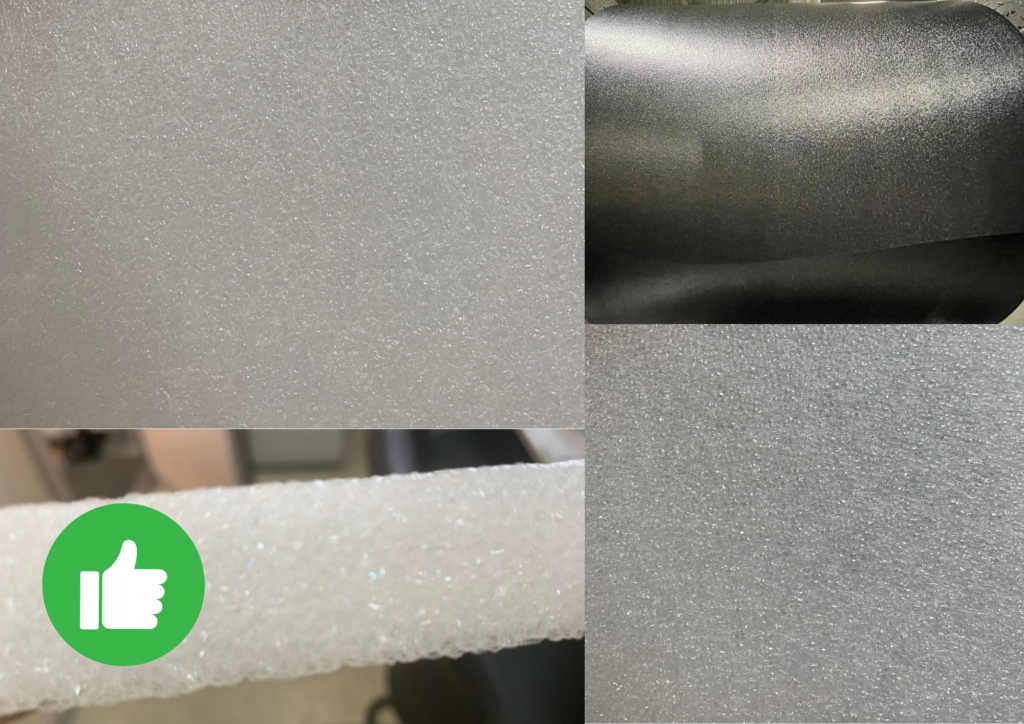
Let’s examine the following three main factors that help you to avoid the common mistakes:
How GMS Affects Surface Tension During Foam Expansion
GMS is a crucial element in cell formation
During the foaming process, surface tension plays a crucial role. It refers to the physical effect that occurs when the blowing agent (such as butane, CO₂, or others) expands under heat inside the extruder. This phenomenon happens precisely when the blowing agent stops flowing and begins forming new foam cells at the point of critical expansion, stretching the walls of already existing cells.
The additive GMS (glycerol monostearate) helps reduce surface tension during this phase, facilitating smoother and more controlled cell formation. By lowering resistance on the cell walls, GMS improves the structural development of the foam, leading to more stable, uniform, and high-quality results.
GMS and Degassing: Controlling Gas Diffusion in Foam
Increasing the amount of GMS (glycerol monostearate) in the formulation can enhance the foam expansion process, but it also introduces several challenges. A high concentration of GMS tends to migrate from the lower layers of the foam to the upper layers, which creates a barrier to gas replacement with air. This results in:
- Longer conditioning times for rolls stored in the warehouse
- Foam structure rupture due to post-production gas expansion
- Formation of irregular or damaged cells
- Potential reduction in lamination quality caused by gas residues and surface GMS buildup
On the other hand, an insufficient GMS concentration can lead to the premature release of gas before the foam has properly stabilized, often resulting in foam collapse during or after production.
This is why it is essential to control GMS dosing accurately through production testing and technical experience. Avoiding both excess and deficiency ensures optimal foam structure, stability, and future lamination performance.
Foam Surface Quality: How GMS Reduces Friction and Static
Reduction of static charges on the surface of the foam during the production process - static charges accumulate on the surface of the foam as a result of friction - thus reducing the risk of fire
The lower the density of the foam (kg/m3) and the saturation/gassing of it, the more the GMS will influence these factors.
Preventing Foam Shrinkage and Surface Defects in Low-Density Foams: The Role of GMS Dosing
One of the most common challenges faced by foam manufacturers working with ultra-light, low-density foams is the issue of shrinkage or rapid post-extrusion expansion during the conditioning phase in storage. This often leads to the appearance of surface bubbles, cracks, or breaks that compromise foam quality.
While some producers experiment with additional additives labeled as "Anticolaps", these products typically act in the same way as GMS (glycerol monostearate), offering no added benefit when used together. Thus, their use is generally redundant.
Best Practices for GMS Dosing in Foam Production
The optimal GMS concentration depends on multiple production parameters, including:
- Foam density
- Raw material feed rate (kg/h)
- Ambient temperature and humidity
- Day-night temperature fluctuations during storage and handling
Given these variables, accurate GMS dosing is essential for maintaining a stable foam structure and preventing post-production defects. A data-driven, experience-based approach to dosing ensures consistent quality and performance in PE and PP foam production.
We are not just an foam machinery designer & manufacturer, we are a developer of technological solutions.
Looking for a reliable partner in PE and PP foam extrusion?
Trust FAP’s experience in custom foam machinery and process optimization.
Contact us today to improve your production quality and reduce waste.