What are the most common technologies used in foam extruders for the production of non-cross linked physical expansion foam in polyethylene (or polypropylene)?
We can highlight 4 most famous technologies: Single Screw Foam Extruder, Tandem Foam Extruder, Twin Co-rotating Screws Foam Extruder & Twin Counter-rotating Screws Foam Extruder.
In the production process of expanded (foam) materials, factors of speed, pressure, temperature, cooling and mixing must be extremely precise in order to obtain perfect mixing combinations. Therefore, the equipment supplied with the foam machine and its crucial parts must be designed in order to have an extremely rapid and flexible response that allows instant optimization of what the foam production process requires.
And here are some of the reasons why FAP has chosen for over 35 years to design and construct 100% «Made in Italy» counter-rotating twin screw foam extruders. So we have decided to share with you and describe some of the great advantages of our foam extrusion lines.
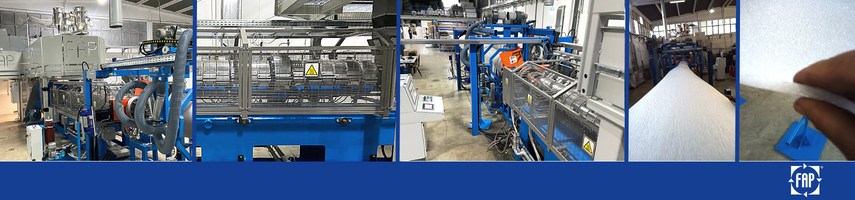
Some facts about the foam extruder and foam extrusion process by FAP:
- All components in granules are distributed at the entrance of the machine by the extremely precise gravimetric dosing station except the gas which is injected in the centre of the foam extruder machine.
- The foam machine never works "full mouth", the machine works in filling controlled by the flow rate of the dosing station and the speed of rotation of the screws. This process allows you to adjust the pressures of the mixture depending on the quantity and speed.
- The mixing is ensured by the mechanical work of the screw profiles which act by crushing the mixture at the point of contact of the screw profiles, and by reversing the mixture in the screw profiles, during the advancement of the mixing;
- The internal cooling is ensured by a circulation of water at controlled temperature, close to the screws and very reactive to the change of temperature setpoints!
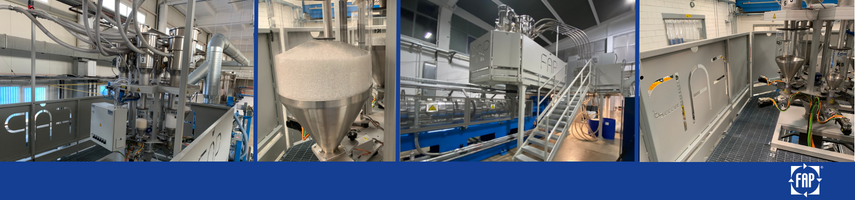
Advantages of FAP’s twin screw counter-rotating extruder for foam production
- Due to flexibility only one twin screw counter-rotating extruder can produce a whole range of materials from ultra-light foams to high thickness foams of various densities!
- The production capacities of foam extruder are adjustable in a proportion of 400% and it is declared the fastest machine for start-up «from ZERO».
- The FAP's counter-rotating process allows very rapid flow and density changes, all parameters can be changed in a few seconds, changes in colorants or gas rate are obtained in a few minutes (5 minutes for gas 7 minutes for talk or colors)!
- The foam technology by twin screws makes possible to obtain better mixing of compositions at a lower melt pressure during homogenization, which leads to a reduction in the risk of damage to the polymer structure under the influence of surface tension.
- The very special profiles of the FAP extruder screw also with specially selected treatmentsand accurate pressure distribution allow the breaks minimizing in the polymer flow during mixing, permit the better control of the temperature of the polymer mass due to less friction and the heat generated, as a result obtaining a very positive effect on the process mixing the polymer mass with gas and further expansion process.
- High-quality mixing of compositions during homogenization, also reduction of friction and overpressure described in points above, have a very positive effect on the distribution of GMS (Glycerol Monostearate) on the foam surface after production, preventing GMS to rise into the upper layers of the foam completely, thus, the foam expansion process is more stable in the first 48 hours after production, the risk of cell wall tearing is significantly reduced, and the process of replacing gas with air in the cell occurs much faster.
- Compared with other well-known foam technologies, only FAP's foam extruder has longer gas expansion zones in the polymer and a sharply critical foam cooling zone This makes it possible to create an expansion of GSE (Gas Structural Element) much more evenly without damaging the polymer grid structure, obtaining a lower density with a greater thickness of the material, as well as to cool and stabilize the process of gas expansion, minimizing the risks of thinning the walls of GSE.
- This technology allows the foam manufacturer to use a smaller amount of gas diffusion stabilizers (example: Anticollapse additive), based on production needs for degassing and expansion, as well as the density of the polymer.
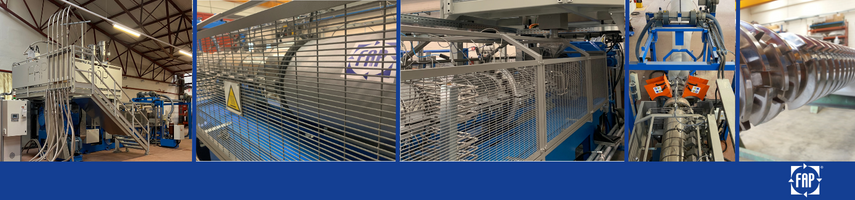
All our machines are just like our children: as they "win" in competitions, we feel like proud parents, conscious of their prowess.
– FAP
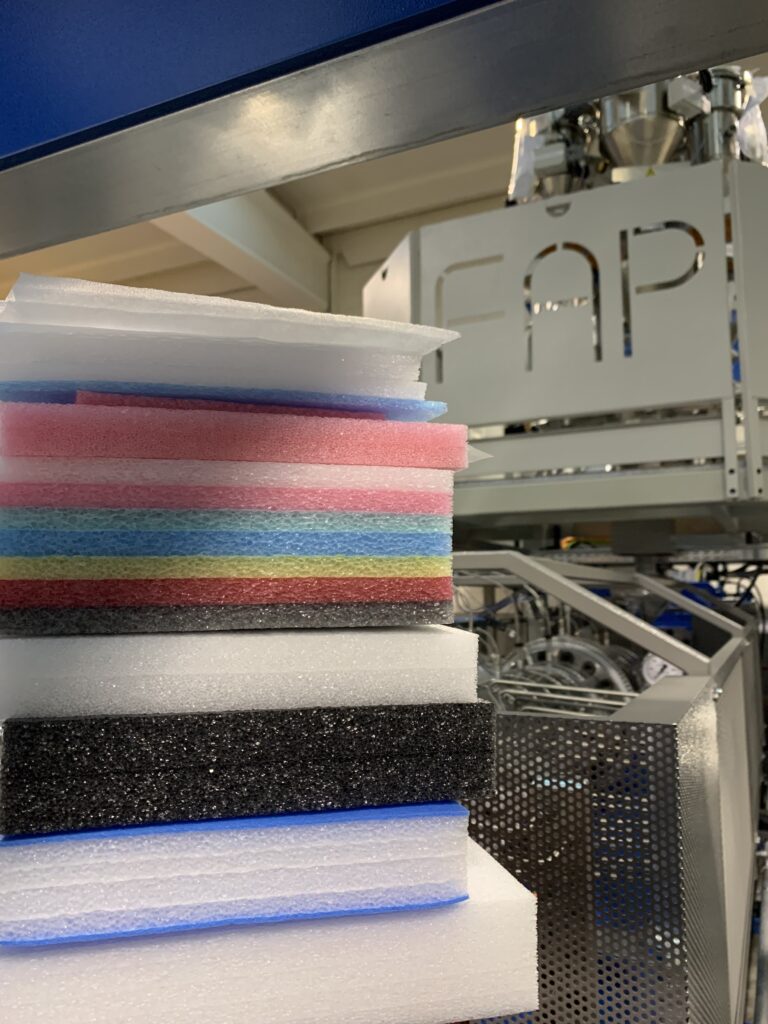